Ein Schädel in sechs Stunden
Vor einer Operation ist jede Information über den Patienten wertvoll. Individuelle 3-D-Modelle von Organen bilden ab, was die Chirurgen im Innern vorfinden werden. Workshops am ARTORG Center der Uni Bern demonstrierten die Vorteile dieser Technologie.
Und plötzlich erhält alles eine andere Dimension: So druckt der Drucker, der an der Stauffacherstrasse 78 im Untergeschoss steht, nicht zweidimensionale Bilder – sondern produziert räumliche Figuren in allen Farben. Der grosse, kastenförmige Apparat mit der Aufschrift «Spektrum Z510» ist ein 3-D-Drucker, mit welchem am «ARTORG Center for Biomedical Engineering Research» der Universität Bern Modelle von Organen und Körperteilen geformt werden. Dieses Verfahren kommt ursprünglich aus der Industrie und heisst «Rapid Prototyping», die schnelle Herstellung von Prototypen für die unterschiedlichsten Anwendungen. An einer Tagung erfuhren kürzlich Kliniker und Ärztinnen, welches Potenzial diese technischen Möglichkeiten für die moderne Medizin bergen.
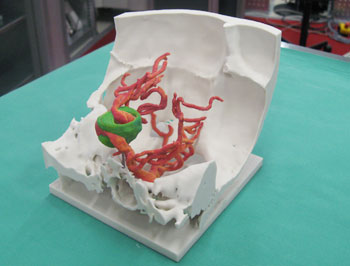
«Photoshop» für klinische Daten
Die «ausgedruckten» Modelle können den Chirurginnen und Chirurgen einen wichtigen Vorteil bieten. «Sie helfen bei der präzisen Planung einer Operation», erklärt Stefan Weber, Kodirektor der Abteilung für Computer gestützte Chirurgie am ARTORG Center. Am Modell können die Ärzte nämlich schon vor dem Eingriff studieren, was sie auf dem OP-Tisch vorfinden werden. Dies ist möglich, da Modelle aufgrund individueller Daten eines Patienten hergestellt werden. Weber führt die zugrunde liegende Idee aus: Digitale Daten aus Tomographien, Röntgenaufnahmen des Patienten, werden am Computer «mit einem Photoshop für klinische Daten» aufbereitet, der Ausschnitt der gewünschten Körperpartie wird selektioniert und der Druckauftrag weitergeleitet. Schon druckt «Spektrum Z510» innerhalb von rund sechs Stunden einen ganzen Modell-Schädel eines bestimmten Menschen in den gewünschten Farben und Grösse aus.
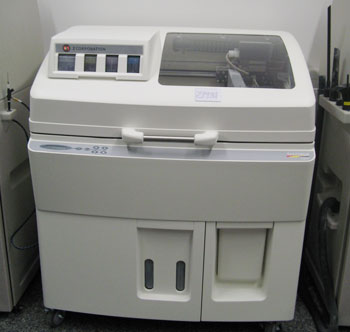
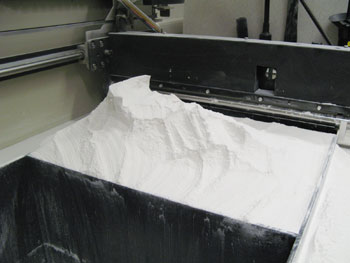
Hilfreich bei der OP-Planung
Weber veranschaulicht noch weiter: Ein Blutgefäss im Gehirn einer Patientin ist erweitert, wie vorgängige bildgebende Verfahren zeigen. Doch nur das geprintete Modell dieses Hirnabschnitts mit seiner ganzen komplexen Gefässstruktur gibt den Neurochirurgen ein plastisches 3-D-Bild, wie die Situation im Kopfinnern der Patientin tatsächlich aussieht. «Aufgrund eines solchen Modells können die Ärzte entscheiden, wie sie vorgehen wollen – reicht ein minimal invasiver Eingriff oder braucht es effektiv eine chirurgische Schädeloperation», so Weber. Gerade in anspruchsvollen Grenzbereichen zwischen Neuroradiologie und Neurochirurgie sei jede zusätzliche Information für den Arzt wertvoll.
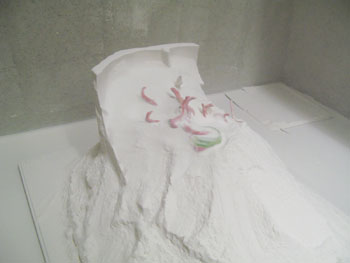
Druck auf feinste Gipsschichten
Eine Information, die in diesem Fall auf dem Prinzip des Tintenstrahldruckers aufgebaut ist: Der 3-D-Drucker verfügt über Patronen aller Farben – ausser schwarz. «Anstelle von schwarz wird beim Drucken Kleber eingespiesen», sagt Ingenieur Weber. Leim und Farben werden auf die feinen, 1/10 Millimeter dicken Schichten von pulverisiertem Gips aufgetragen, den ein automatischer Schieber kontinuierlich heranbringt und planiert. Mit jeder Schicht rückt der Schieber mit dem Gips-Lager hinauf, die geklebte und gefärbte Figur wächst und wächst. «Ist der Vorgang abgeschlossen, kann das Modell aus dem Gipspulver-Haufen gegraben werden», sagt Weber. Ein Anstrich mit Giessharz verhindert zum Schluss, dass das Modell zu bröckeln beginnt.
Auf Wunsch wird ein Modell aus Zellulose erstellt. Die kleinen Hohlräume dieser porösen Materie werden anschliessend mit Polyurethan, einem Kunststoff, aufgefüllt: «Danach kann die Zellulose herausgebrochen werden und wir erhalten ein elastisches Modell eines Herzens oder eines Ohrs», sagt Stefan Weber.